ProDec decontamination technique
During plant turnaround when columns and vessels are exposed to atmosphere, the presence of hydrocarbon residues, coke and pyrophoric iron sulfide contribute the most to fire hazard during mechanical works. ProDec minimizes the fire hazard during decontamination works by converting pyrophoric iron sulfide into inert iron sulfate salt, and delivers high assurance of safety for maintenance works when dealing with both fire hazards and H2S issues.
ProDec application would employ either steam circulation or soaking technique for decon activities depending on the target unit and facilities configuration. Pressurized steam will be used as a media to carry out the decon works. In order to facilitate the decon works and minimized the complexity of the decon activities, ProDec application has been designed to follow on site plant's steaming route and procedures. The decon shall start with the preparation of ProDec well before the actual job, with sludge sample taken from the equipment to perform decon works. This is the ensure that ProDec will be fully optimized for the requirement. The period of circulation required depeds on the ProDec ratio and the right operating temperature. Generally ProDec is applied by circulation technique for a period between 8-12 hours. In normal practive for a CDU, ProDec is injected through stripping steam line and at several identified point at the column and associated loops. A concenptual diagram of ProDec decon application on CDU is shown below:
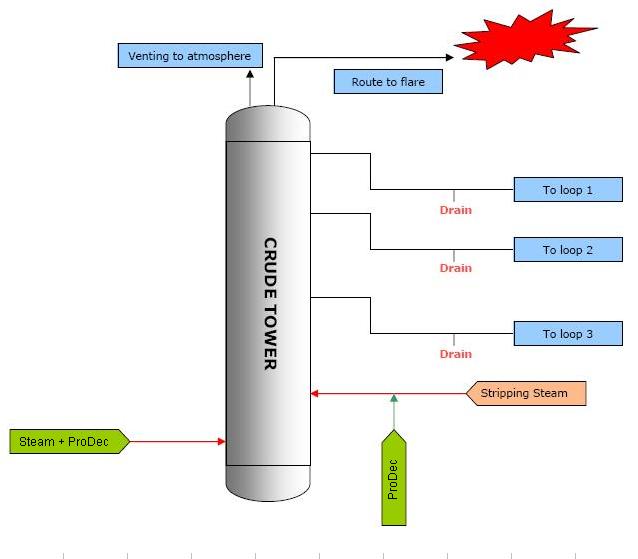
Step 1
Determination of the actual amount of ProDec to employ. A typical rule of thumb is to take 1-3% of the tower volume depending on the system dynamics. Crude tower and its associated loops will be pre-heated at least 1 hour in order to obtain the desired temperature (100ºC). Then all first contaminants will be routed to the flare and drained at the lowest point.
Step 2
When the desired temperature is achieved, ProDec will be injected through stripping steam at several designated injection points. Typically medium pressure steam of 3.5 - 7 bar is employed.
Step 3
The mixture of steam and ProDec enters the column as an atomized mist of cloud. As the mixture expands to fill up the volume and space inside the tower, the mixture will agitate, scrub, encapsulate and strip all contaminants and stubborn soil into micro-emulsion. This mixture will be circulated for 8 - 12 hours with LEL readings being taken at regular interval at selected nozzles. Upon confirming that the LEL levels have reduced to zero, this mixture will then be carried to the flare, vented to atmosphore and carry over to the condensate during draining activity.
Step 4
The final waste shall be managed by the plant operator to dispose at their Effluent Treatment System (ETS). From the previous history, ProDec chemical and its by-product did not contribute to any adverse effect to the ETS. The sludge and soild part of the waste can be safely collected into drums and sent for scheduled waste disposal.